* Reading Tips:
To reduce reader fatigue, this article will be divided into two parts (Part 1 and Part 2).
This [Part 2] contains 1341 words and is expected to take 8-10 minutes to read.
1. Introduction
Mechanical grinders and polishers ( hereinafter referred to as "grinders and polishers" ) are equipment used to grind and polish the surface of workpieces. They are widely used in the surface treatment of various materials such as metals, wood, glass, and ceramics. Grinders and polishers can be divided into many types according to different working principles and application scenarios . Understanding the major categories of mechanical grinders and polishers , their characteristics, applicable scenarios, advantages and disadvantages, is crucial for choosing the right grinding and polishing equipment.
2. Classification and characteristics of mechanical grinding and polishing machines
[ Based on the applicable classification of workpiece appearance (material, shape, size) ] :
2.1 Handheld grinder and polisher
2.2 Benchtop grinding and polishing machine
2.3 Vertical grinding and polishing machine
2. 4 gantry grinding and polishing machine
2.5 Surface grinding and polishing machine
2.6 Internal and external cylindrical grinding and polishing machines
2.7 Special grinding and polishing machine
In the previous article, we shared some chapters 1-2.7 of the first half of the framework. Now we continue: |
[ Division based on operational control requirements (accuracy, speed, stability) ] :
2.8 Automatic grinding and polishing machine
2.8.1 Features :
- High degree of automation and high production efficiency.
- It can realize automatic feeding, automatic grinding and polishing , and automatic unloading.
- Suitable for mass production, saving labor costs.
2.8.2 Applicable scenarios:
Automated grinding and polishing machines are suitable for surface treatment of workpieces produced in large quantities, such as electronic product casings, home appliance parts, etc.
2.8.3 Comparison of advantages and disadvantages:
advantage |
shortcoming |
High degree of automation and high production efficiency |
Complex maintenance and high requirements for operator training |
Save labor costs |
The equipment price is high |
Suitable for mass production |
Limited scope of application |
Mechanical grinding and polishing machines, in addition to fully automated equipment, also have manual operation and processing systems that are highly dependent on human labor, and semi-automated equipment that is in between. The choice depends on factors such as the production efficiency of the workpiece, precision requirements, labor cost and management ratio control, and economy (which will be shared later).
Figure 8: Schematic diagram of an automated grinding and polishing machine
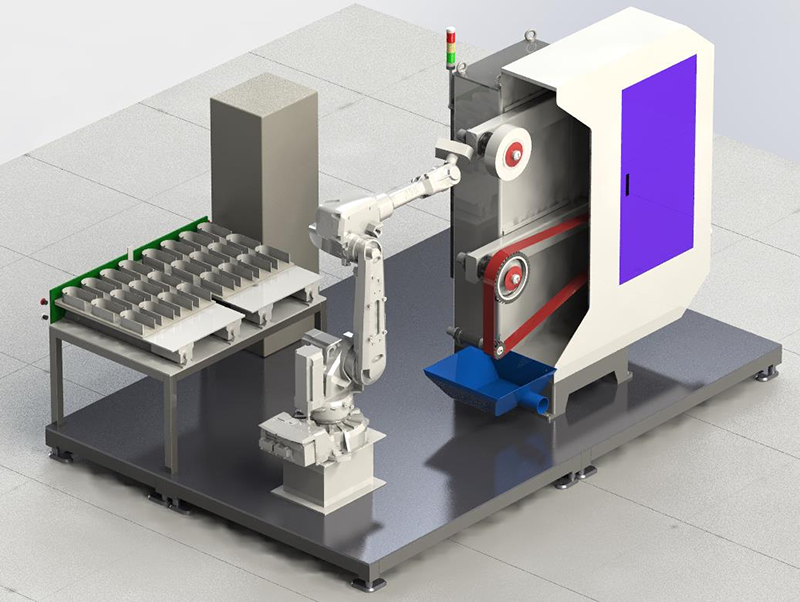
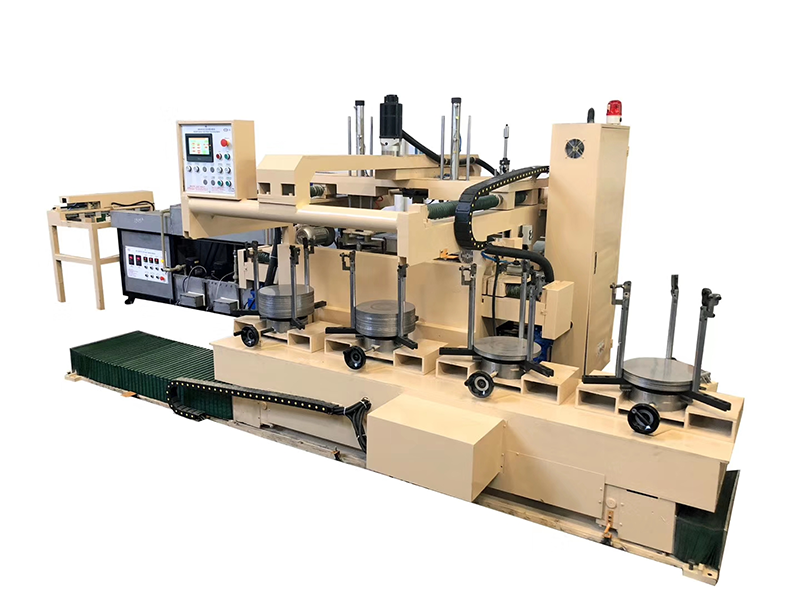
2.9 CNC grinding and polishing machine
2.9.1 Features :
- Using CNC technology, high precision.
- It can realize high-precision grinding and polishing of workpieces with complex shapes .
- Suitable for high-demand, high-precision surface treatment.
2.9. 2 Applicable scenarios:
CNC grinding and polishing machines are suitable for surface treatment of high-precision and high-requirement workpieces, such as aviation parts and precision instruments.
2.9.3 Comparison of advantages and disadvantages:
advantage |
shortcoming |
High precision, suitable for workpieces with complex shapes |
The equipment price is high |
Good grinding and polishing effect, high degree of automation |
The operation is complicated and requires professional training |
Suitable for high-precision surface treatment |
Complex maintenance |
Figure 9: Schematic diagram of CNC grinding and polishing machine
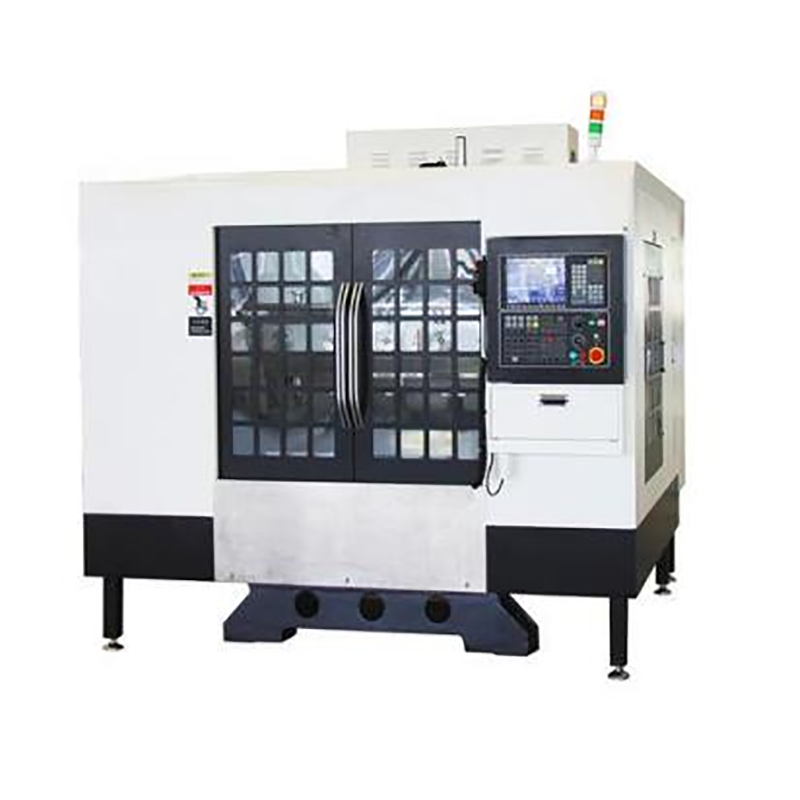
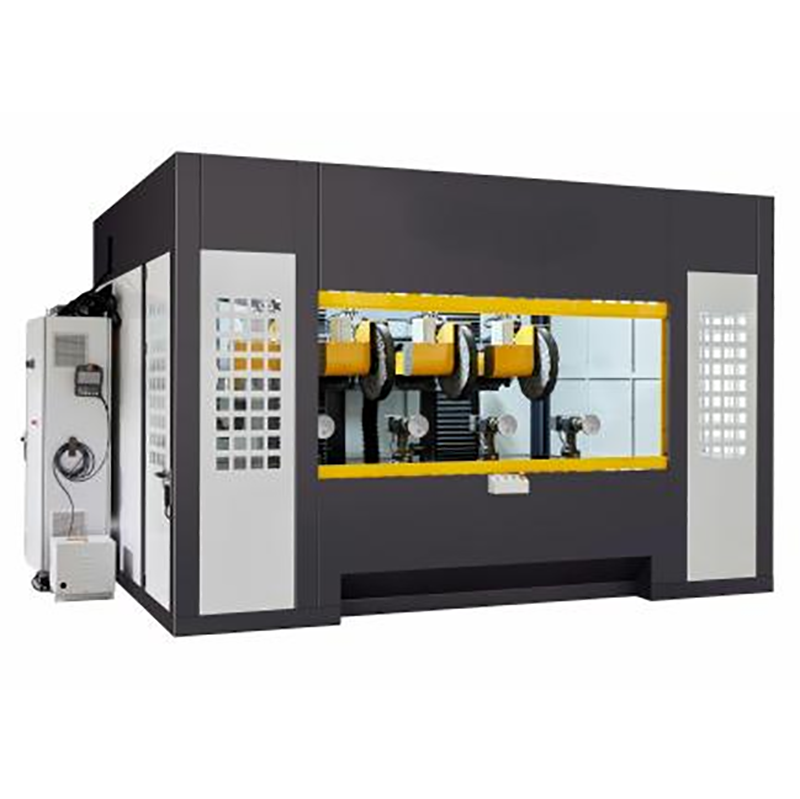
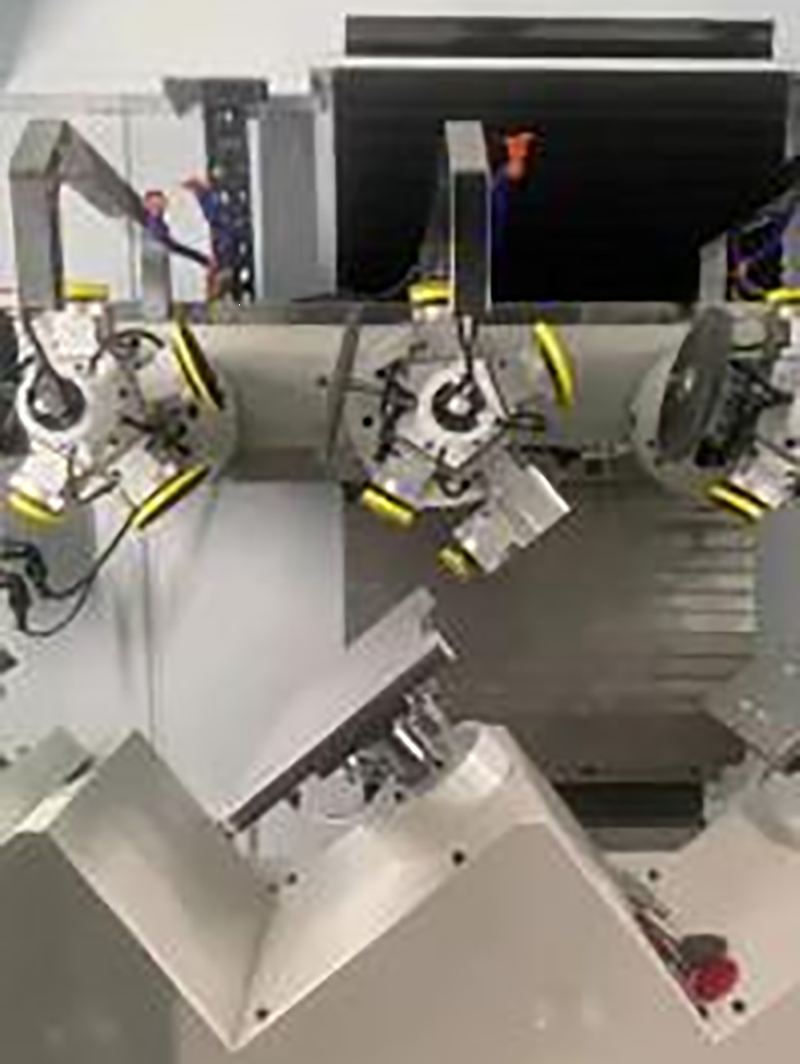
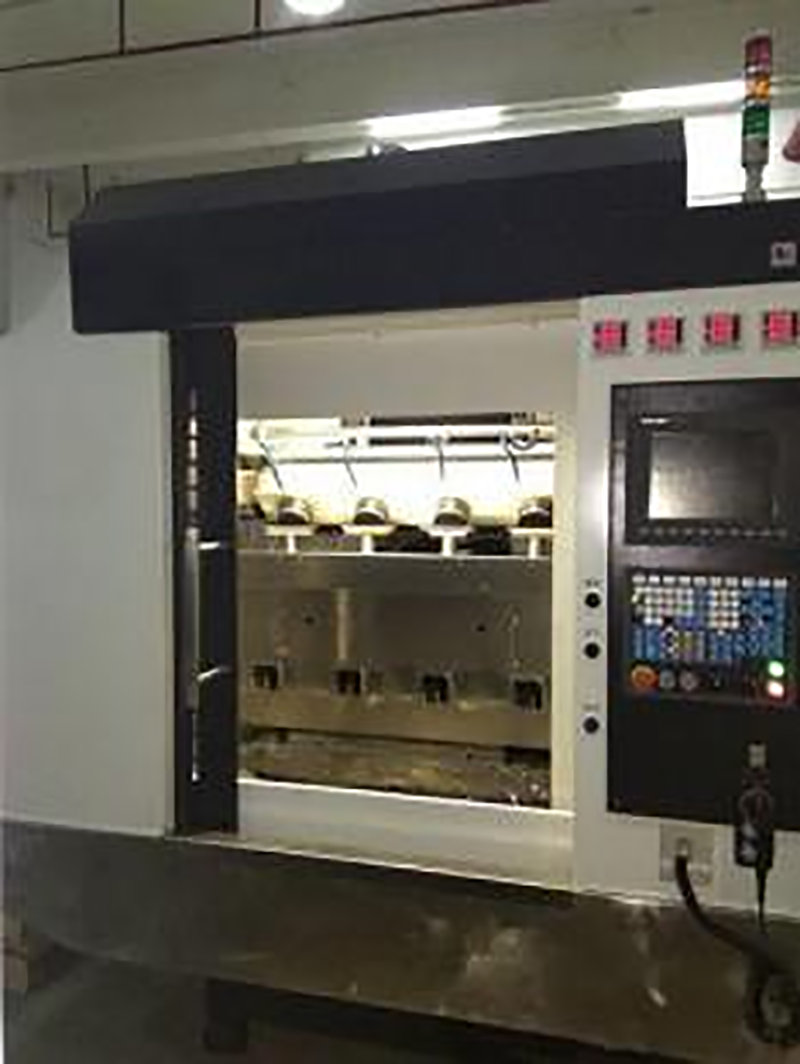
3. Cross-comparison of models in different categories
In the actual purchasing process, enterprises should choose the most suitable grinding and polishing machine model based on their own production needs, process requirements and budget, so as to improve production efficiency and product quality and promote the sustainable development of the enterprise.
Grinding and polishing machine type |
Features |
Applicable scene |
advantage |
shortcoming |
Handheld grinding and polishing machine |
Small size, light weight, flexible operation | Small area, local grinding and polishing | Easy to carry, suitable for workpieces with complex shapes | grinding and polishing efficiency, requiring high operating skills |
Table type grinding and polishing machine |
Compact structure, small footprint | Grinding and polishing of small and medium-sized workpieces | High precision, simple operation and easy maintenance | grinding and polishing capabilities, narrow scope of application |
Vertical grinding and polishing machine |
The equipment has moderate height and high grinding and polishing efficiency | Grinding and polishing of medium-sized workpieces | Easy to operate, good grinding and polishing effect | The equipment occupies a large area and is expensive |
Gantry type grinding and polishing machine |
grinding and polishing large workpieces , with a high degree of automation | Grinding and polishing of large workpieces | Good stability, suitable for mass production | The equipment is large and expensive |
Surface grinding and polishing machine |
Suitable for surface treatment of flat workpieces | Grinding and polishing of flat workpieces | grinding and polishing effect, suitable for high-precision surface treatment | Only suitable for flat workpieces, slow grinding and polishing speed |
Internal and external cylindrical grinding and polishing machine |
Suitable for grinding and polishing the inner and outer surfaces of cylindrical workpieces with high efficiency | Grinding and polishing of cylindrical workpieces | grinding and polishing of internal and external surfaces is possible | The equipment structure is complex and the price is high |
Special grinding and polishing machine |
Designed for specific workpieces, highly applicable | Grinding and polishing of workpieces with special shapes or complex structures | Strong targeting, good grinding and polishing effect | Equipment customization, higher price |
Automatic grinding and polishing machine |
High degree of automation, suitable for mass production | Grinding and polishing of workpieces for mass production | Save labor costs and high production efficiency | The equipment is expensive and maintenance is complicated |
CNC grinding and polishing machine |
Adopting CNC technology, suitable for high-precision and complex workpiece surface treatment | High-precision workpiece grinding and polishing | High precision, suitable for workpieces with complex shapes | The equipment is expensive and requires professional training |
3.1 Accuracy comparison
CNC grinding and polishing machines and automatic grinding and polishing machines have obvious advantages in terms of precision and are suitable for surface treatment of high-precision workpieces. Handheld grinding and polishing machines are flexible to operate, but their accuracy is greatly affected by operating skills.
3.2 Efficiency comparison
Gantry-type grinding and polishing machines and automated grinding and polishing machines have outstanding performance in terms of efficiency and are suitable for mass production. Handheld grinding and polishing machines and desktop grinding and polishing machines are suitable for small batch production or local grinding and polishing , and the efficiency is relatively low.
3.3 Cost comparison
Handheld grinding and polishing machines and desktop grinding and polishing machines are relatively low-cost and suitable for small processing plants or personal use. CNC grinding and polishing machines and automated grinding and polishing machines are more expensive, but can significantly improve production efficiency and product quality, and are suitable for use by large enterprises.
3.4 Applicability comparison
Handheld grinders and polishers are suitable for grinding and polishing small-area, complex-shaped workpieces ; desktop grinders and polishers are suitable for batch grinding and polishing of small and medium-sized parts ; vertical grinders and polishers and internal and external cylindrical grinders and polishers are suitable for surface treatment of medium-sized and cylindrical workpieces; gantry grinders and polishers are suitable for surface treatment of large workpieces; plane grinders and polishers are suitable for surface treatment of plane workpieces; special grinders and polishers are suitable for grinding and polishing of workpieces with special shapes or complex structures ; automated grinders and polishers are suitable for mass production; CNC grinders and polishers are suitable for surface treatment of high-precision, high-requirement workpieces.
Post time: Jul-10-2024