* Reading Tips:
To reduce reader fatigue, this article will be divided into two parts (Part 1 and Part 2).
This [Part 1] contains 1232 words and is expected to take 8-10 minutes to read.
1.Introduction
Mechanical grinders and polishers ( hereinafter referred to as "grinders and polishers" ) are equipment used to grind and polish the surface of workpieces. They are widely used in the surface treatment of various materials such as metals, wood, glass, and ceramics. Grinders and polishers can be divided into many types according to different working principles and application scenarios . Understanding the major categories of mechanical grinders and polishers , their characteristics, applicable scenarios, advantages and disadvantages, is crucial for choosing the right grinding and polishing equipment.
2. Classification and characteristics of mechanical grinding and polishing machines
[ Based on the applicable classification of workpiece appearance (material, shape, size) ] :
2.1 Handheld grinder and polisher
2.2 Benchtop grinding and polishing machine
2.3 Vertical grinding and polishing machine
2. 4 gantry grinding and polishing machine
2.5 Surface grinding and polishing machine
2.6 Internal and external cylindrical grinding and polishing machines
2.7 Special grinding and polishing machine
[ Division based on operational control requirements (accuracy, speed, stability) ] :
2.8 Automatic grinding and polishing machine
2.9 CNC grinding and polishing machine
2.1 Handheld grinder and polisher
2.1.1 Features :
- Small size and light weight, easy to carry and operate.
grinding and polishing small area or complex shape workpieces .
- Flexible operation, but requires high operating skills.
2.1.2 Applicable scenarios:
Handheld grinders and polishers are suitable for small-area, local grinding and polishing work, such as surface repair of cars and motorcycles, polishing of small furniture pieces, etc.
2.1. 3 Advantages and disadvantages comparison chart:
advantage |
shortcoming |
Flexible operation and easy to carry |
grinding and polishing efficiency, limited scope of application |
Suitable for workpieces with complex shapes |
Requires higher operating skills |
Relatively low price |
Easy to produce operator fatigue |
Figure 1: Schematic diagram of a handheld grinder and polisher
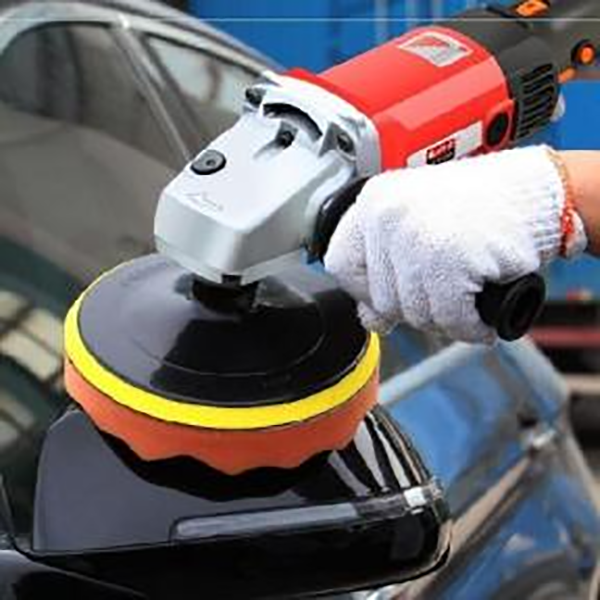
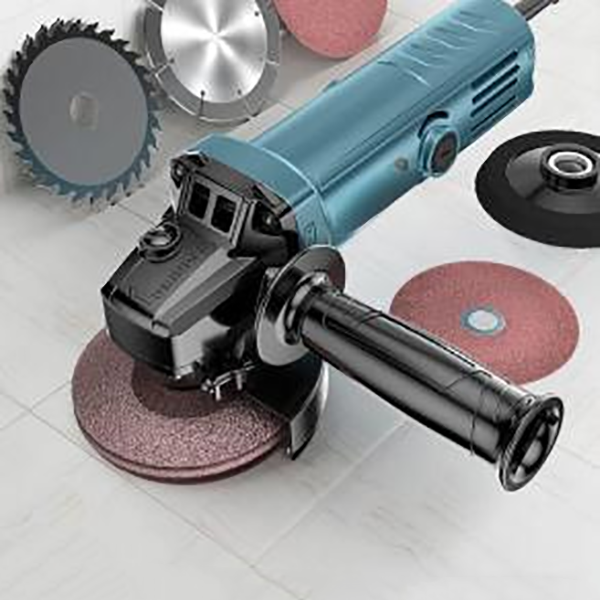
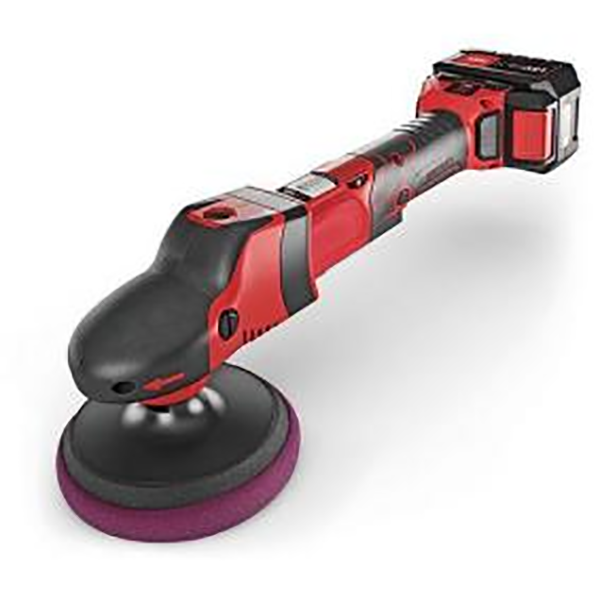

2.2 Benchtop grinding and polishing machine
2.2.1 Features :
- The equipment has a compact structure and occupies a small area.
- Suitable for batch grinding and polishing of small and medium-sized workpieces .
- Simple operation, suitable for small processing plants.
2.2. 2 Applicable scenarios:
Desktop grinders and polishers are suitable for surface grinding and polishing of small and medium-sized parts , such as small metal parts, watch accessories , jewelry , etc.
2.2. 3 Advantages and disadvantages comparison chart:
advantage |
shortcoming |
The equipment has compact structure, high precision and small footprint |
The grinding and polishing capacity is limited and the application scope is narrow |
Simple operation and easy maintenance |
Not suitable for large workpieces |
fair price |
Low degree of automation |
Figure 2: Schematic diagram of a benchtop grinder and polisher
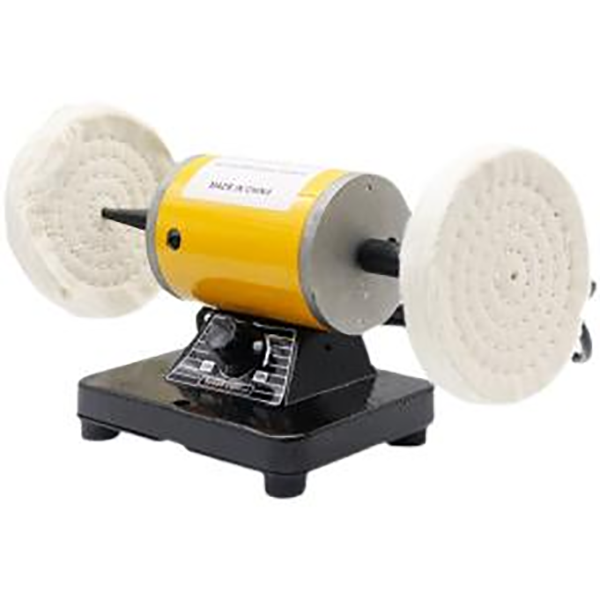
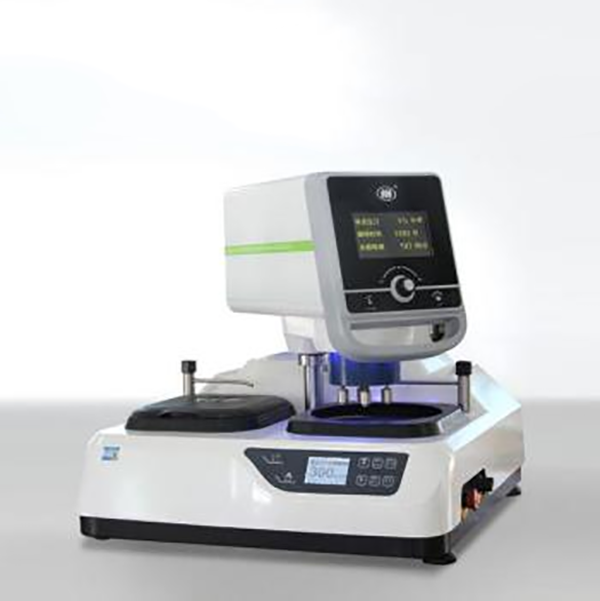
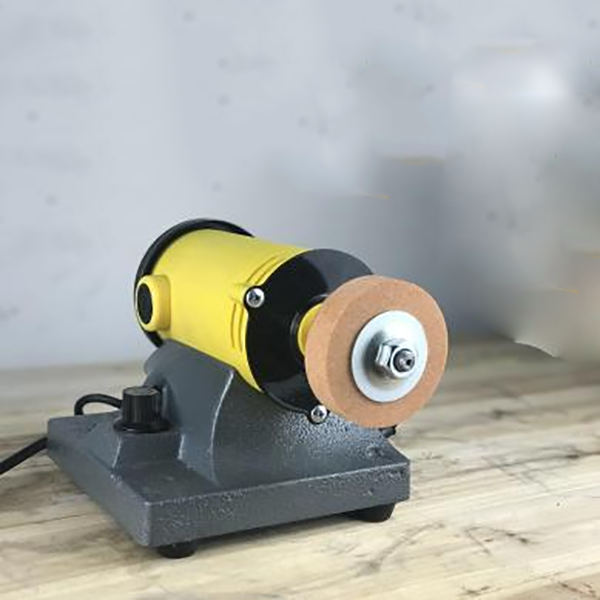
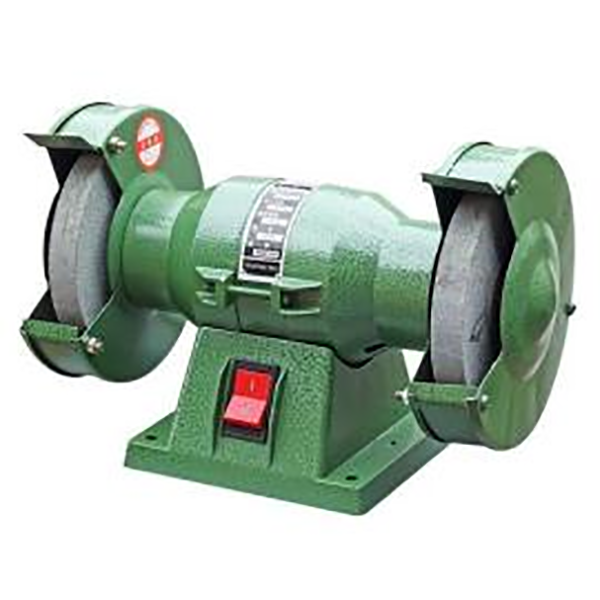
2.3 Vertical grinding and polishing machine
2.3.1 Features :
- The equipment is at a moderate height and easy to operate.
- Suitable for surface grinding and polishing of medium-sized workpieces .
- The grinding and polishing efficiency is high, suitable for small and medium-sized processing enterprises.
2.3.2 Applicable scenarios:
Vertical grinding and polishing machines are suitable for surface treatment of medium-sized parts, such as tools, mechanical parts, etc.
2.3.3 Comparison of advantages and disadvantages:
advantage |
shortcoming |
Moderate operating height for easy operation |
The equipment occupies a large area |
High grinding and polishing efficiency |
Limited scope of application |
Easy maintenance |
Relatively high price |
Figure 3: Schematic diagram of vertical grinding and polishing machine
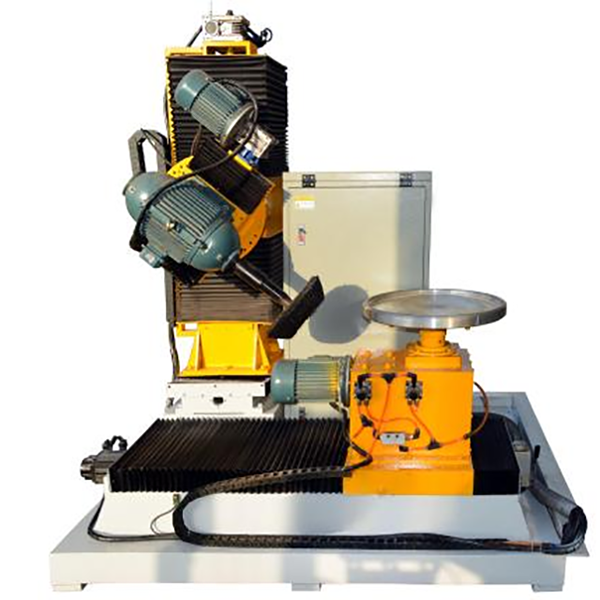
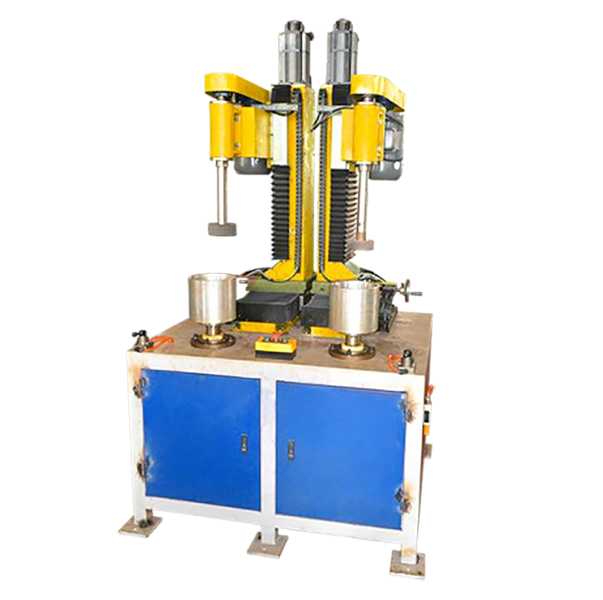
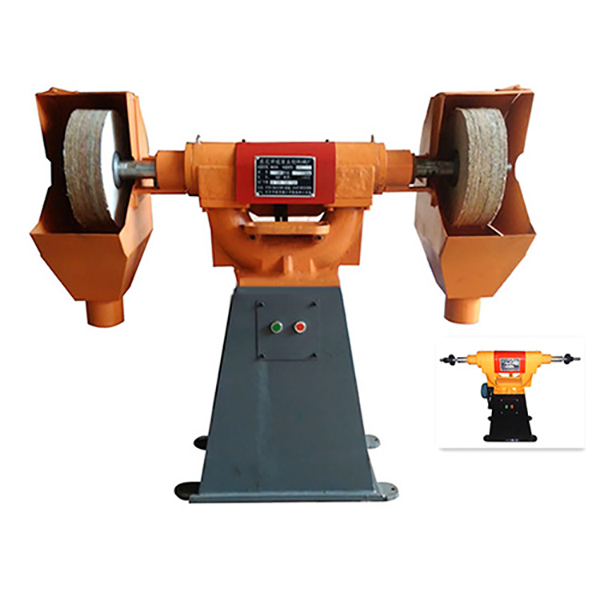
2. 4 gantry grinding and polishing machine
2.4.1 Features :
grinding and polishing large workpieces .
- Gantry structure, good stability and uniform grinding and polishing effect.
- Suitable for mass production with high degree of automation.
2.4.2 Applicable scenarios :
Gantry type grinding and polishing machine is suitable for surface treatment of large workpieces, such as ship parts, large molds, etc.
2.4.4 Comparison of advantages and disadvantages :
advantage |
shortcoming |
Good stability and uniform grinding and polishing effect |
The equipment is large in size and occupies a large area |
High degree of automation, suitable for mass production |
Higher price, complex maintenance |
Suitable for large workpieces |
Limited scope of application |
Figure 4 : Schematic diagram of a gantry type grinding and polishing machine
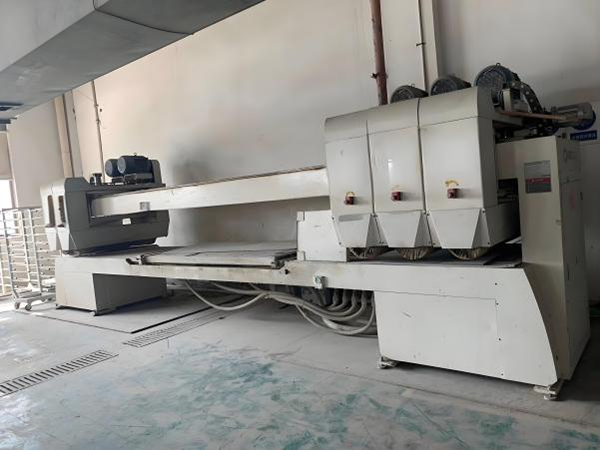
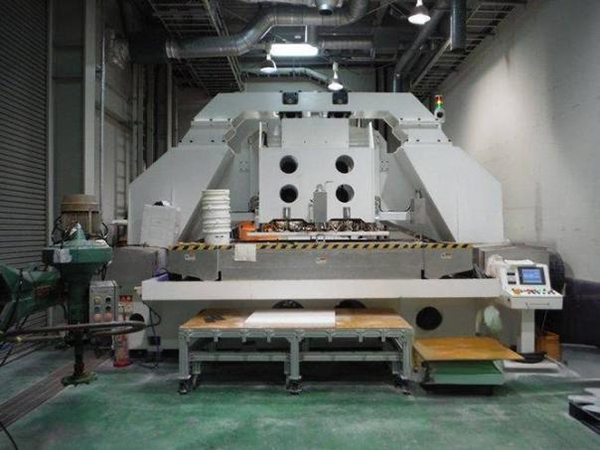
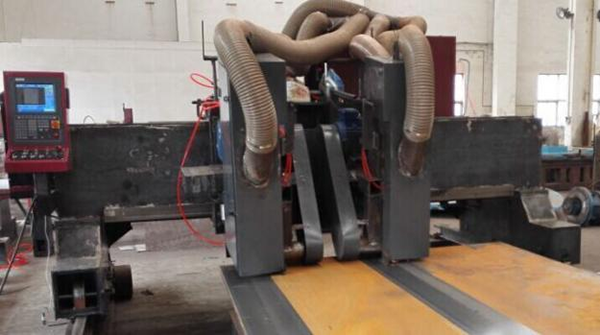
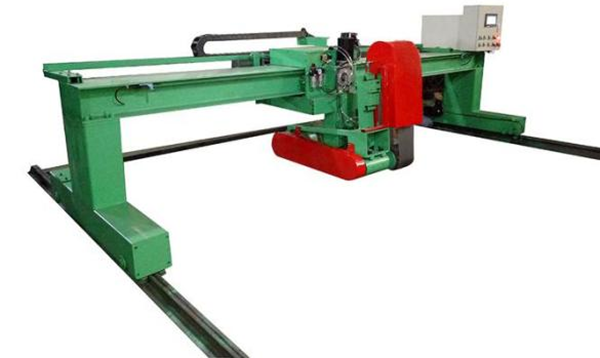
2.5 Surface grinding and polishing machine (small and medium area)
2.5.1 Features :
- Suitable for surface grinding and polishing of flat workpieces .
-Good grinding and polishing effect, suitable for high-precision surface treatment.
- The equipment has simple structure and easy operation.
2.5. 2 Applicable scenarios:
Surface grinding and polishing machines are suitable for surface treatment of flat workpieces, such as metal sheets, glass, ceramics, etc.
According to the size and shape of the workpiece plane, it can be divided into:
2.5. 2.1 Single plane grinder and polisher: Plate grinder and polisher
2.5. 2.2 Multi-plane grinding and polishing machines for general areas: square tube grinding and polishing machines, rectangular grinding and polishing machines, quasi-rectangular & R angle grinding and polishing machines, etc.;
2.5.3 Comparison of advantages and disadvantages:
advantage |
shortcoming |
Good grinding and polishing effect, suitable for high-precision surface treatment |
Only applicable to external flat workpieces |
The equipment has simple structure and is easy to operate. |
Faster grinding and polishing speed |
fair price |
Relatively complex maintenance |
Figure 5: Schematic diagram of a surface grinding and polishing machine
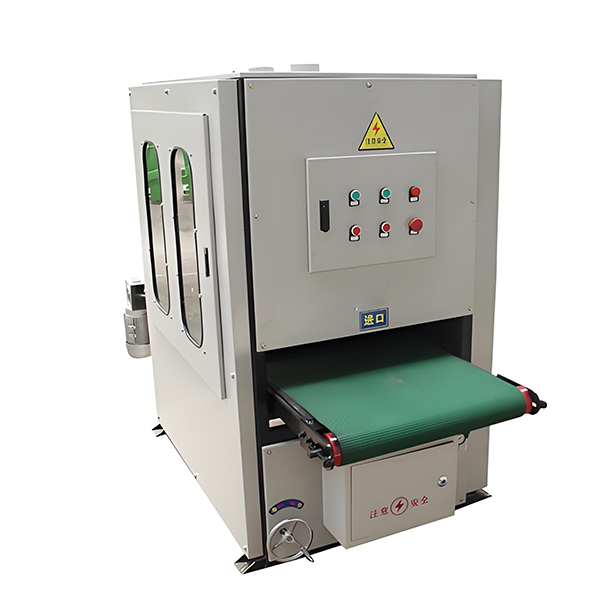
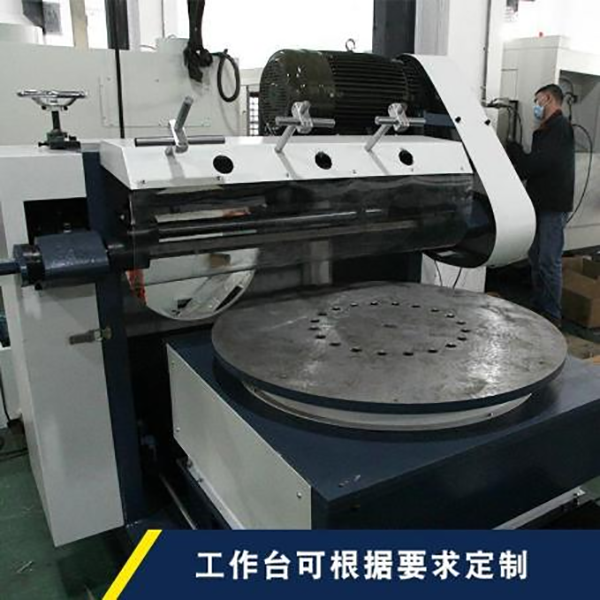
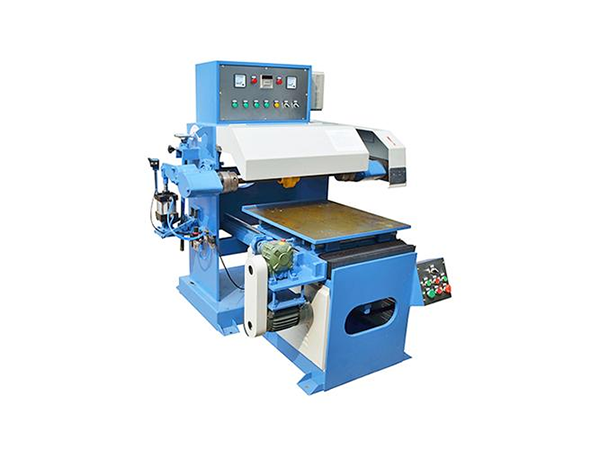
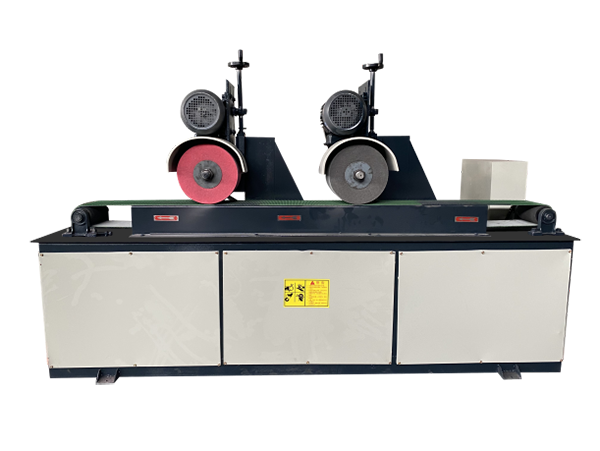
2.6 Internal and external cylindrical grinding and polishing machines
2.6.1 Features :
- Suitable for grinding and polishing the inner and outer surfaces of cylindrical workpieces .
- The equipment has reasonable structure and high grinding and polishing efficiency.
- It can grind and polish the inner and outer surfaces at the same time , saving time.
2.6.2 Applicable scenarios:
Internal and external cylindrical grinding and polishing machines are suitable for surface treatment of cylindrical workpieces, such as bearings, pipes, etc.
2.6.3 Comparison of advantages and disadvantages:
advantage |
shortcoming |
grinding and polishing efficiency, capable of simultaneously grinding and polishing the inner and outer surfaces |
The equipment structure is complex and difficult to maintain |
Suitable for cylindrical workpieces |
Higher price |
Uniform grinding and polishing effect |
Limited scope of application |
Figure 6: Schematic diagram of internal grinding and polishing machine
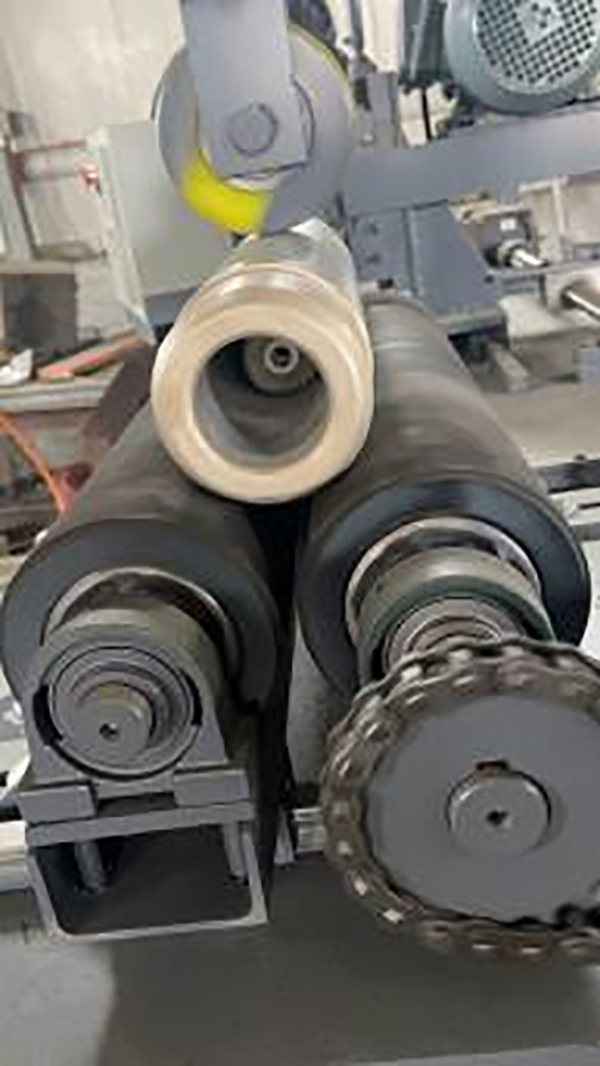
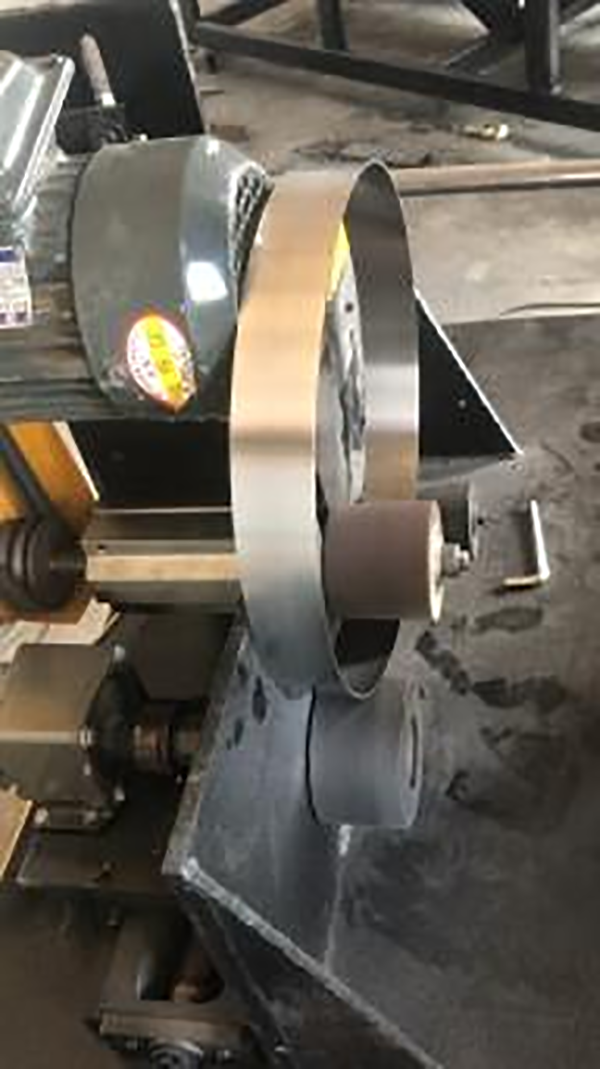
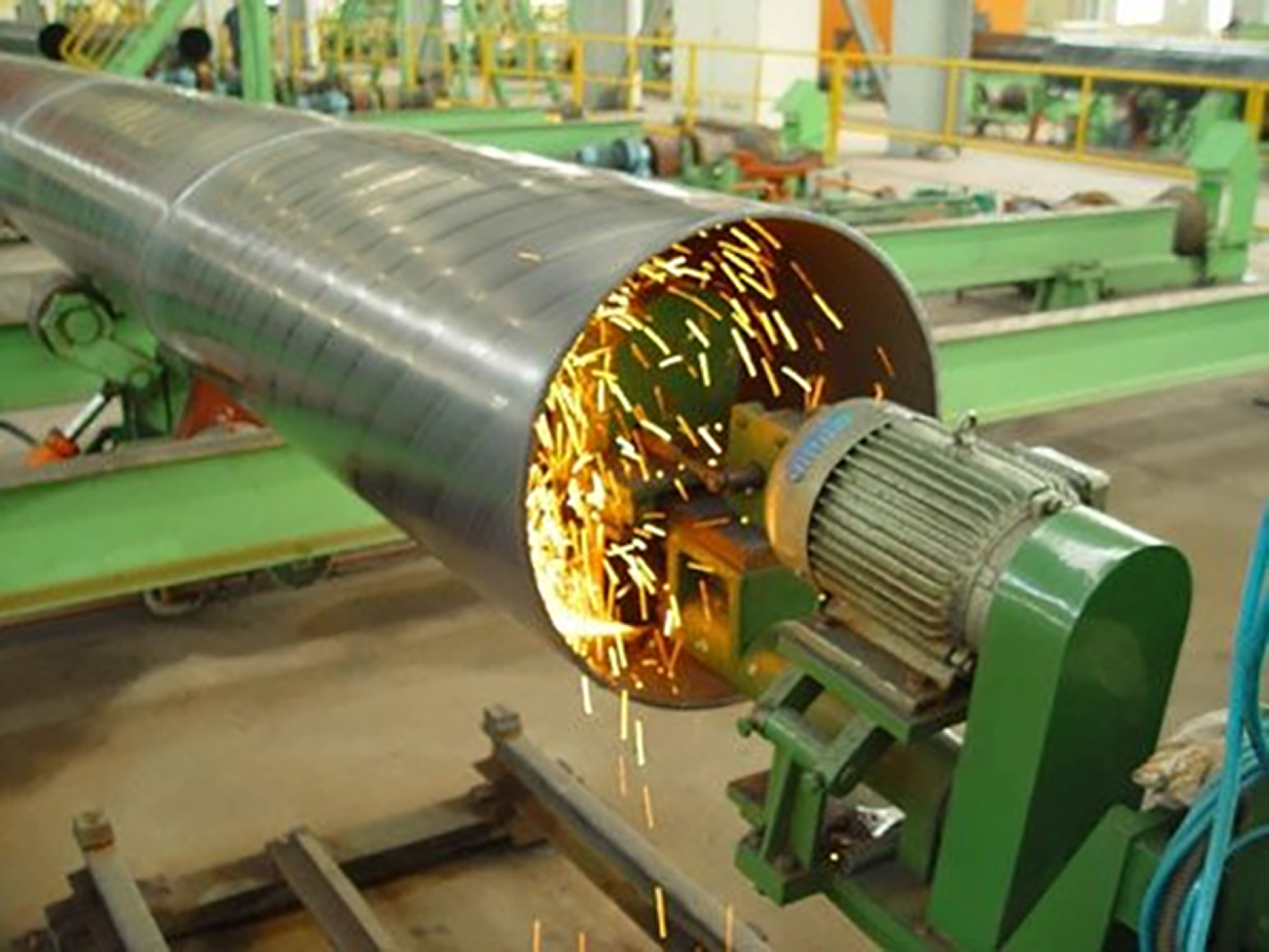
Schematic diagram of external cylindrical grinding and polishing machine :
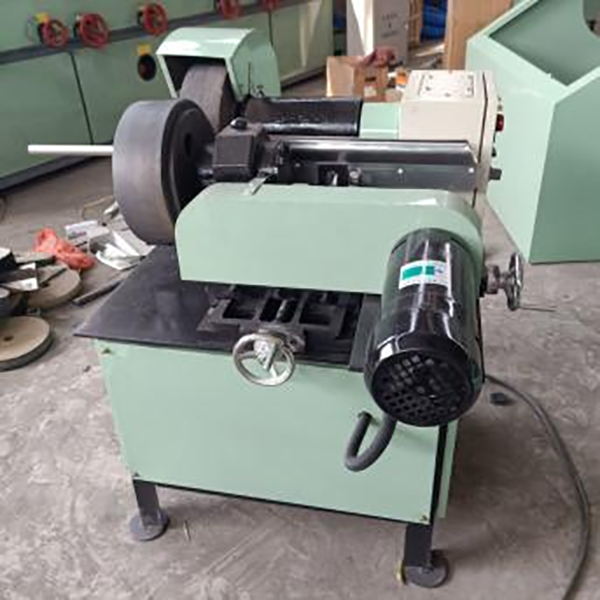
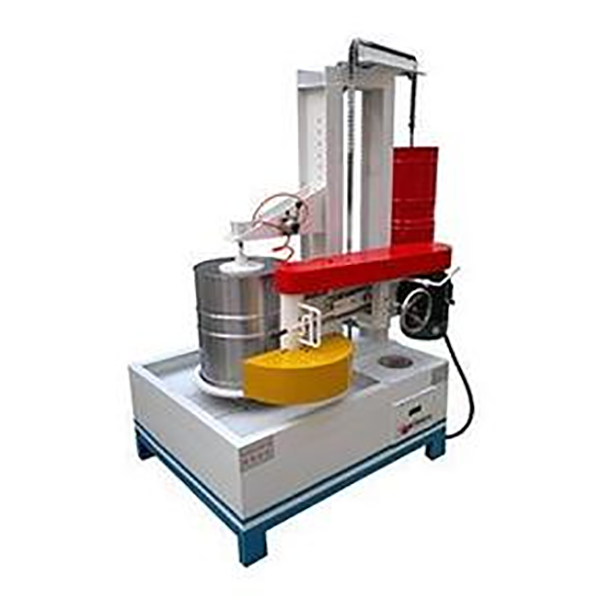
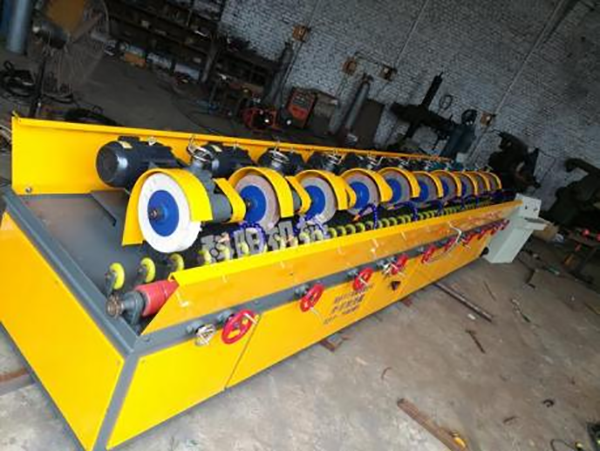
2.7 Special grinding and polishing machine
2.7.1 Features :
- Designed for specific workpieces, with strong applicability.
- Equipment structure and function are customized according to workpiece requirements.
- Suitable for grinding and polishing workpieces with special shapes or complex structures .
2.7. 2 Applicable scenarios:
Special grinding and polishing machines are suitable for surface treatment of specific workpieces, such as automotive parts, medical equipment, etc.
2.7.3 Comparison of advantages and disadvantages:
advantage |
shortcoming |
Strong targeting, good grinding and polishing effect |
Equipment customization, higher price |
Suitable for workpieces with special shapes or complex structures |
Narrow scope of application |
high degree of automation |
Complex maintenance |
Figure 7: Schematic diagram of a dedicated grinding and polishing machine
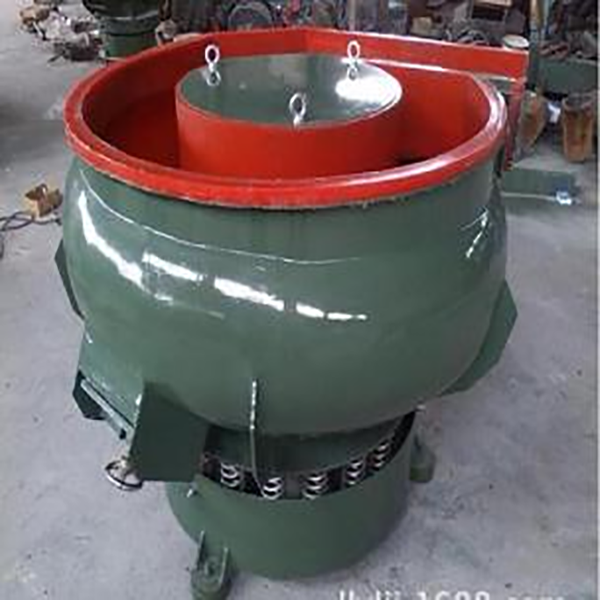
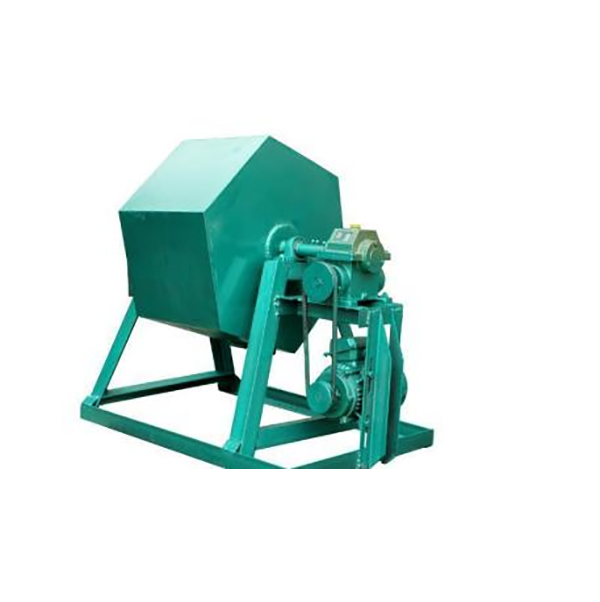
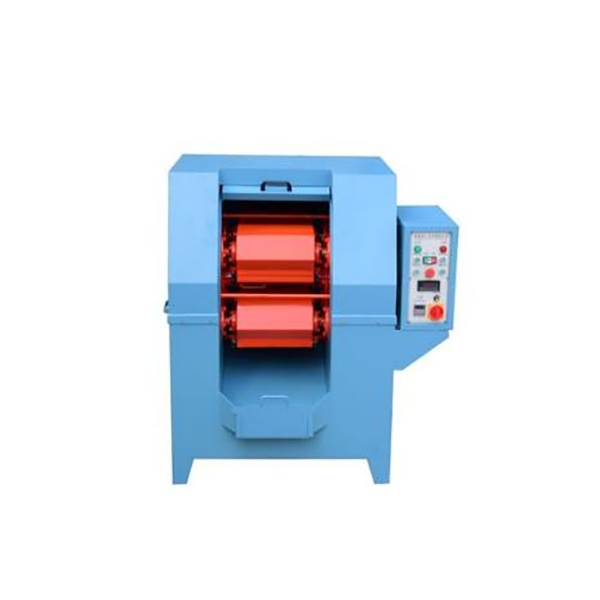
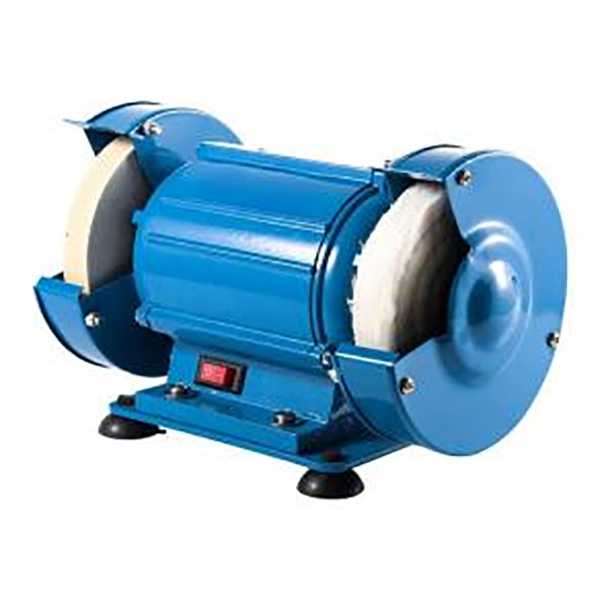
(To be continued, please read 《How to choose a grinder and polisher correctly [Mechanical grinder and polisher special topic ] Paty2 》)
【Subsequent Contents Framework of ‘Paty2’】:
[ Division based on operational control requirements (accuracy, speed, stability) ]
2.8 Automatic grinding and polishing machine
2.9 CNC grinding and polishing machine
3. Cross-comparison of models in different categories
3.1 Accuracy comparison
3.2 Efficiency comparison
3.3 Cost comparison
3.4 Applicability comparison
[Conclusion]
What are the core factors that affect the purchase of mechanical grinding and polishing machines?
Haohan Group is one of the leading grinding and polishing machine manufacturers and customized solution providers in China. It has about 20 years of experience in focusing on various types of mechanical grinding and polishing equipment . And it is worthy of your trust!
[Contact now, register your information]: HYPERLINK "https://www.grouphaohan.com/" https://www.grouphaohan.com
Post time: Jul-02-2024