A butter machine is a machine that adds butter to a car, also called a butter filling machine. The butter machine is divided into pedal, manual and pneumatic butter machine according to the pressure supply method. The foot butter machine has a pedal, which provides pressure by the feet; the manual butter machine provides pressure by repeatedly pressing the pressure rod on the machine up and down by hand; the most commonly used is the pneumatic butter machine, and the pressure is provided by an air compressor. The butter machine can be fed into a car or other mechanical equipment that needs to be filled with butter through a hose through pressure.
The working principle of the butter machine is to drive the air motor with compressed air, drive the piston to reciprocate, and use the area difference between the upper and lower ends of the piston to obtain high-pressure fluid output. The output pressure of the liquid depends on the area ratio across the piston and the pressure of the driving gas. The area ratio of the two ends of the piston is defined as the area ratio of the pump and is marked on the model of the pump. By adjusting the working pressure, fluids with different pressure outputs can be obtained.

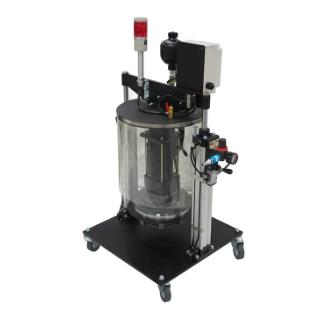
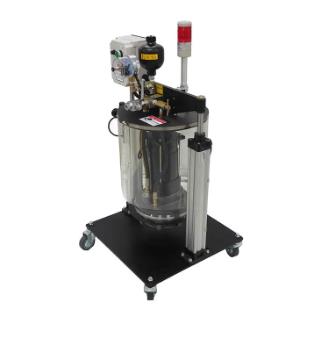
Another notable feature of the butter filling machine is that the pump starts and stops completely automatically. When the butter machine is working, it can start automatically by opening the oil gun or valve; when it stops, as long as the oil gun or valve is closed, the butter machine will automatically stop.
The gear oil pump works with two gears intermeshing and rotating, and the requirements for the medium are not high. The general pressure is below 6MPa, and the flow rate is relatively large. The gear oil pump is equipped with a pair of rotary gears in the pump body, one active and the other passive. Relying on the mutual meshing of the two gears, the entire working chamber in the pump is divided into two independent parts: the suction chamber and the discharge chamber. When the gear oil pump is running, the driving gear drives the passive gear to rotate. When the gears are engaged to disengaged, a partial vacuum is formed on the suction side, and the liquid is sucked in. The sucked liquid fills each tooth valley of the gear and is brought to the discharge side. When the gear enters the meshing, the liquid is squeezed out, forming a high-pressure liquid and discharged out of the pump through the pump discharge port.
Generally, the thicker the lubricating pipeline, the smaller the resistance, so when selecting the oil pipeline, it is necessary to choose a pipeline that is appropriately thicker; or shorten the length of the branch pipeline as much as possible. In addition, when targeting the above-mentioned customers, the restriction and influence of dust and comprehensive management level on the implementation of lubrication management should also be considered.
Through experimental comparison, the lubrication methods that are suitable for my country's shipping machinery requirements are as follows:
1. Fully automatic computer program-controlled lubrication system
2. Manual point-by-point valve-controlled lubrication system
3. 32MPa multi-point direct supply lubrication system (if DDB multi-point direct supply type is selected, special consideration should be given to the problem of pipeline pressure drop in winter). 4. The manual distributor lubrication system is suitable for the lubrication of small starting machinery whose total resistance does not exceed 2/3 of its standard pressure.
There are also many types of butter pumps in life, one of which is a device called an electric butter pump. So what are the maintenance measures for this equipment?
1. The pressure regulation of the compressed air should not be too high, otherwise the elegant hose will be damaged due to the overload of the equipment, which will affect the service life of the high-pressure hose. It is generally recommended that the pressure regulation should not exceed 0.8 MPa.
2. Always clean and maintain the equipment regularly, clean the entire oil circuit system regularly, remove the oil nozzle from the oil injection gun, and reciprocate several times with clean oil to flush out the debris in the pipeline, and keep the oil storage tank inside. Oil cleaning.
3. When the electric grease pump is started, check the fuel tank first. Do not start the machine with no load for a long time when the oil in the oil storage tank is insufficient, so as to avoid the heating of the plunger oil pump and damage to the parts.
4. During the operation of the electric grease pump, the compressed air components are often filtered when necessary. In order to avoid some dust and sand falling into the air pump of the electric grease pump, causing the wear of some parts such as the cylinder, and causing damage to the internal parts of the electric grease pump.
5. When the electric grease pump is damaged and must be dismantled and repaired, it must be dismantled and repaired by professionals. The dismantling and repairing must be proper, and the accuracy of the dismantled parts cannot be damaged, and the surface of the parts can be avoided.
Post time: Oct-14-2022