Both wire drawing and polishing belong to the surface treatment industry, and they are similar to a certain extent. They both use mechanically driven consumables to process materials in contact, and use contact pressure and friction to achieve processing results. In the classification of polishing wheels in the previous chapter, we carried out according to the process. In this chapter, the drawing consumables mainly divide the drawing consumables into drawing abrasive belts and drawing wheels.
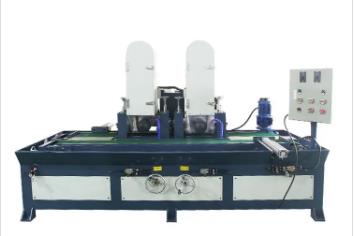
The brushed abrasive belt, which forms an annular belt outside, is mainly used for skin grinding and wire drawing. There are also many kinds of abrasive belts, which are generally classified according to the thickness of the surface, and the number of abrasive belts is strictly divided according to the thickness.
Often when drawing a product, we need to select the appropriate number of abrasive belts according to the hardness of the product material and the technological requirements of the product. Using the same type of abrasive belt to process stainless steel and aluminum, the depth and thickness of the texture will vary. has a difference. If we want to sand a gold casting product, the surface of the product is relatively rough, and the gold casting material is hard, then we generally choose a coarser abrasive belt. In fact, before the craftsman determines the type of abrasive belt used for processing a certain product, he often tries to use several types of abrasive belts that are closer to the sample, and selects the type of abrasive belt used for the best effect as the final process standard.
The wire drawing wheel, with a round shape, is mainly used for wire drawing, and some wire drawing wheels can also be used for polishing. The wire drawing wheel has the same function as the abrasive belt, but there are differences in the processing method. The abrasive belt often uses multi-wheel drive to drive the abrasive belt drive for trial operation in the product contact drawing, while the wire drawing wheel uses the rotating contact wire drawing, the effect is the same, but the processing technology is different. Our commonly used wire drawing wheels include thousand impellers, thousand wire wheels, nylon wheels, flying wing wheels and so on. The first two kinds of drawing wheels are actually modified versions of abrasive belts, with the same material, but they are changed to the form of wheels to facilitate rotary processing. The latter two are mainly used for wire drawing processing with higher technological requirements, and are often used in the wire drawing of the casings of some high-end digital products such as mobile phones and computers. In addition, the processing of the wire drawing wheel has special requirements for the machine. If the wheel-shaped consumables rotate at high speed, the polishing effect will often be formed, otherwise, high temperature combustion may occur. Therefore, the use of wire drawing machinery often requires low speed, or frequency conversion control of the machinery, "high-speed polishing, low-speed wire drawing" is a common term in the industry.
In fact, in our production practice, we often inadvertently find that some other methods can also achieve the drawing effect, and the consumables used may be very simple. For example, the most commonly used hemp wheel and hemp rope wheel in stainless steel polishing, we adopt a certain speed control in polishing, and can achieve the effect of broken grain and wire drawing without waxing. For another example, it is also our common round tube polishing. When we carry out the rough sand passing process, we use the grinding wheel to rotate the sand, and the round tube at this time has a wire drawing effect of the circle pattern. So, time will make countless new discoveries, and it will also solve many problems that we think are very complicated.
Post time: Oct-25-2022